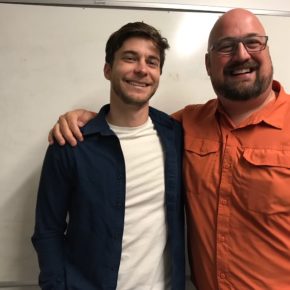
Smarter Sorting’s Scott Mackey, vice president of sustainability, and Chris Ripley, CEO and founder.
He struck up a conversation with her and discovered she worked at the City of Austin‘s Resource Recovery Center and was learning to recycle paint. Together, they went to the center and Ripley ended up volunteering his expertise as a paint maker there for nine months.
One day he wanted to get some paint solvent from a Drum Storage Container behind a red line, only to discover he was not allowed to touch the “hazardous waste” after people yelled at him. Two Drum Storage Containers were slated to be picked up by a disposal company and sent to an incinerator. The City of Austin paid the company about $5 a gallon to haul off and dispose of the waste. Retailers can pay up to $15 a gallon to dispose of the waste, Ripley said.
Ripley got to use some of the solvents under a re-use policy and that sparked the idea for Smarter Sorting.
Smarter Sorting, based at Galvanize in downtown Austin, takes unwanted consumer chemical products from cities and businesses, primarily retailers, and finds a reuse for them to prevent waste from going up in smoke.
Smarter Sorting, founded in 2017, has closed on $9.3 million in seed funding including $2.5 million from RTP Ventures. The company is using the funds to drive transparency in the chemical waste management industry and to automate environmental compliance processes for retailers. It has created a one of its kind smart chemical database.
Smarter Sorting’s technology gives municipalities, retailers, and waste management companies the ability to accurately identify, categorize and sort every class of chemical-containing product, said Ripley, the company’s founder, and CEO. Next, Smarter Sorting helps to recycle chemical products back into use instead of having them be destroyed.
Smarter Sorting has 30 employees including a team of data scientists and experts behind Wolfram Alpha.
Smarter Sorting’s customers include 17 municipalities nationwide and Canada’s largest retailer, Canadian Tire. And the City of Austin, with its zero waste goal, has partnered with Smarter Sorting to develop its industry-changing technology.
“Everyone using it has experienced substantial savings, both in employee hours needed to sort the waste and in the actual reuse process itself – helping to solve the problem of 1.4 billion pounds of consumer chemical products being incinerated as waste every year,” according to Smarter Sorting.
Just recently, the California Product Stewardship Council awarded Smarter Sorting their most prestigious honor: the Arrow Award for giving cities and retailers the tools they need to identify items that can be reused.
“We are delighted to promote and celebrate California companies who are leaders in driving a circular economy so that nothing is landfilled or incinerated,” Heidi Sanborn, Executive Director of the California Product Stewardship Council, said in a news statement. “I congratulate Smarter Sorting for creating the first database technology that makes it fast scalable and convenient to redirect hazardous products from incineration to reuse.”
“Because of existing compliance and disposal burdens, Smarter Sorting customers save money, increase staff efficiency, and improve their compliance,” according to Ripley.
Smarter Sorting uses a combination of hardware and software to solve the data disconnect to reuse chemical products. The company sends the retailer a machine that scans chemical-based products such as spray paint and cleaners for reuse. Smarter Sorting then takes the products and finds a market for them. Products that have to be destroyed go to an industrial disposal company that incinerates the products.
“We’re the hottest department of weird stuff that is profitable,“ Ripley said.
One of its partners for reuse is Habitat for Humanity.
HFH Home Centers and Smarter Sorting Partnership from Cloudy Logic on Vimeo.
Leave a Reply